récapitulatif de l'avancement
électroniqueboitier : en cours, voir détail ci-dessous
- refaite à l'identique
- fonctionne
- première série de cartes produites, mais mauvaise dimension
- en attente d'un boitier aux bonnes dimensions pour lancer une 2eme série de "prototypes" à la bonne taille
- manque les parties en cuivre de part et d'autre, je cherche une solution
compartiment à pilesbouton rouge
- fini
- reste des détails de l'ordre de 0.1mm à peaufiner
protection transparente
- fini
pièce principale
- modélisée
- pas de prototype réalisé
autocollant
- 1er prototype réalisé
- 2eme prototype réalisé
- des différences mineures sur les faces internes du boitier, qui ne sont visibles qu'une fois démonté
mon imprimante 3D est HS, je dois en racheter une depuis décembre 2023 mais j'ai d'autres priorités sur mon budget...
- je cherche un fournisseur
Comme indiqué dans le titre, je vais vous parler d'un projet de re-fabrication des télécommandes de PLIP de centralisation de nos 205, 309, BX, etc...
![]() | attention : ce projet est encore assez récent, il faudra compter entre 6 mois et 2 ans avant que les re-fabrications soient disponibles | ![]() |
(et non, je ne prends pas de pré-commandes)
Maintenant que vos espoirs sont retombés, et que vous savez que ça va encore prendre du temps, je vais vous dire exactement de quoi il retourne :
je veux concevoir, produire, et proposer à la vente une réplique le plus fidèle possible des télécommandes de PLIP de 205, qu'on trouve encore à des prix affolants en occasion. Cela implique de respecter la couleur du boîtier, sa forme, son assemblage mécanique, sa configuration interne, refaire le circuit imprimé au plus proche en forme, couleur, dimensions, composants.
Pourquoi j'en parle ici ? par ce que j'ai envie de partager cette expérience sans parler de l'aspect commercial. Ce sujet est un fil de discussion autours du projet en lui même, de ce qui se passe super bien, de ce qui ne va pas et qu'il va falloir corriger, de ce que je doit apprendre, ... Et bien sur aussi, si vous avez des idées, ou des pistes pour m'éviter de tâtonner sur certains points... bah ça profitera à tout le monde

J'ai commencé par ce qui me semblait le plus simple, comprendre comment le courant passe dans le circuit imprimé d'origine. J'en ai fait un schéma pour visualiser ça de manière plus conventionnelle, et me suis ensuite attelée à l'autre chose qui me semblait simple : mesurer le circuit imprimé.
Ensuite, il m'a fallu identifier les composants du circuit, trouver leurs références, caractéristiques, et disponibilité.
Avec tout ça, j'avais atteint la limite de mes connaissances avant d'attaquer ce projet (oui, ça fait peu, je suis d'accord).
J'ai donc du apprendre à utiliser un logiciel pour modéliser un circuit imprimé, qui pourra ensuite être commandé via internet à une entreprise spécialisée. Coup de bol, je suis à l'aise avec l'ordinateur, et apprendre un nouveau jeu logiciel est toujours amusant enrichissant

Me voila donc avec ces deux schémas, un pour dire comment passe le courant et lister les composants définitifs, l'autre pour modéliser le circuit imprimé, placer les composants et les relier entre eux.
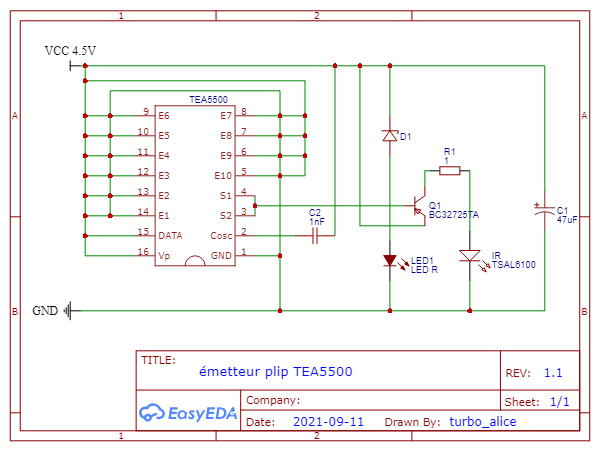
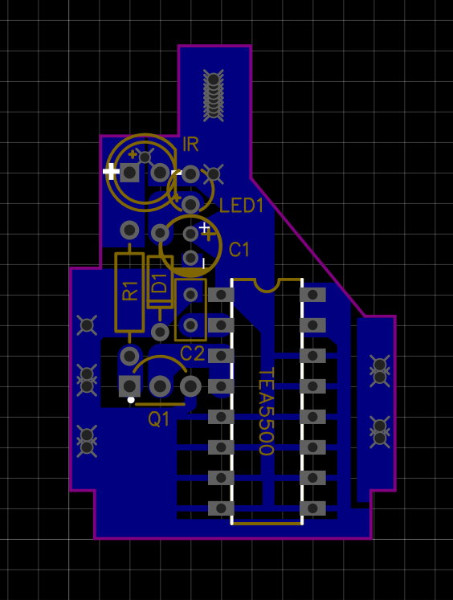
J'ai pu retrouver la moitié des composants avec la même référence qu'à l'origine, mais pour l'autre moitié j'ai du me rabattre sur des équivalents. Ça ne nuira en rien au bon fonctionnement du projet, mais c'est frustrant de se rendre compte qu'on ne pourra pas faire une reproduction aussi fidèle que voulu.
En parallèle, j'ai commencé à réfléchir sur le gros dossier de ce projet pour moi : le boîtier plastique qui va autours du circuit imprimé.
Comment le faire fabriquer, par ce que moi je n'y connais rien en plastique.
Heureusement, j'ai pu botter en touche : avant de le fabriquer, il va bien falloir le modéliser sur ordinateur, ce boîtier ! Oui, mais autant apprivoiser un logiciel d’électronique assez simple, ça va, ... mais affronter un logiciel de conception 3D complet, je me sentais pas de le faire.
J'ai donc utilisé le joker de l'appel à une amie, qui s'y connaît en modélisation 3D, et elle a bien voulu m'aider sur ce projet (ouf !).
Me voila donc de retour avec mon pied à coulisse, à mesurer cette fois ci non pas l'électronique, mais la plastique ! Tant bien que mal, je finis par avoir mes cotes extérieures pour le boîtier, mais le plus dur reste à venir : mesurer l'intérieur pour que l’électronique rentre pile à la bonne place, que la LED tombe en face du trou, ...
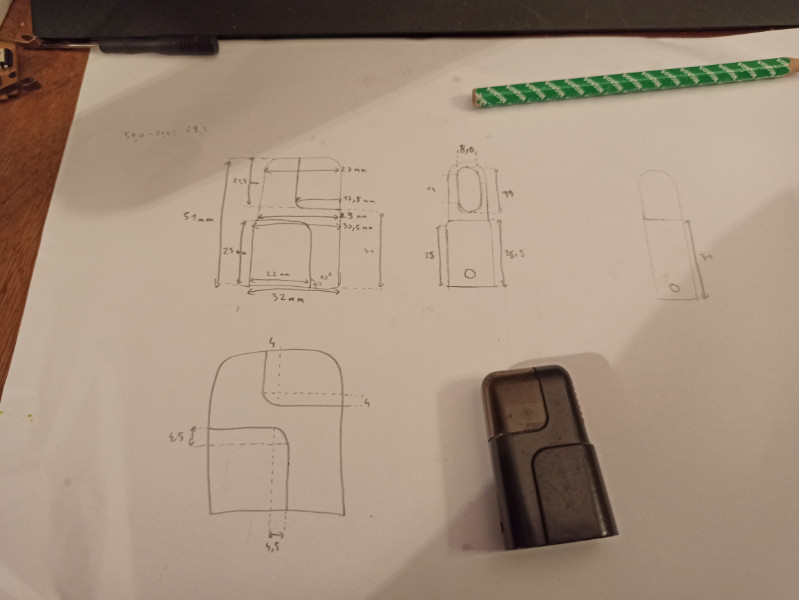
j'ai même eu un assistant pour faire mes mesures...
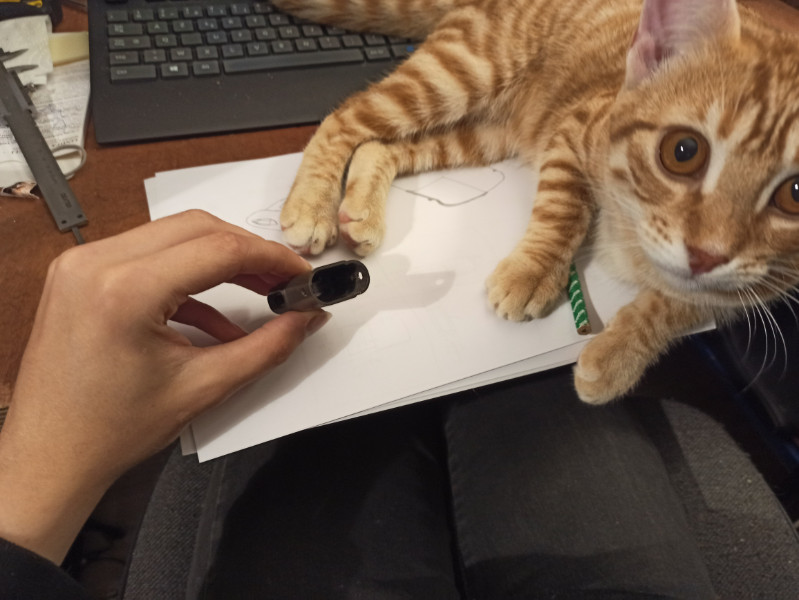
Un appel à l'aide est alors lancé via Facebook, pour trouver un boîtier cobaye à disséquer pour mesurer les organes internes !
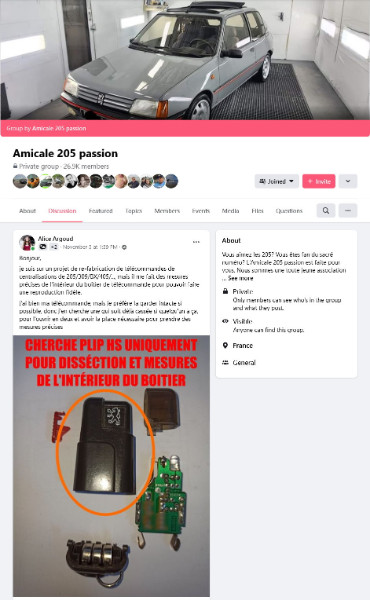
Et miracle : j'ai trouvé une âme charitable qui m'a envoyé le sien cassé en me souhaitant de la réussite pour mon projet

Dissection est donc opérée, le boîtier est coupé en deux sur la longueur afin de mesurer tous les petits reliefs sans trop de complications !
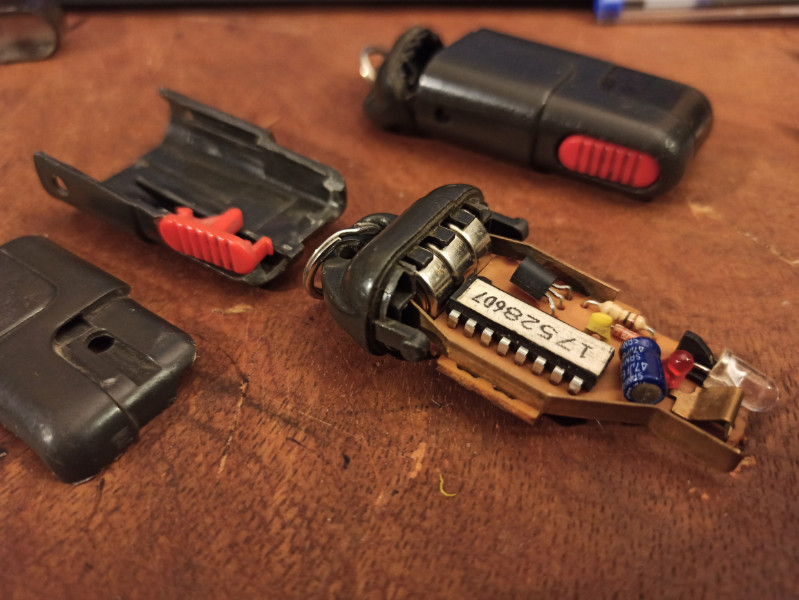
Les mesures sont envoyées à mon joker, qui s'occupe de la modélisation 3D (et de son avis, "ça fait un bien fou de voir toutes ces cotes ! t'as pas idée du nombre de gens qui m'envoient 2 pauvres photos et débrouille toi avec ça !").
Et moi en attendant, je me tourne les pouces ?
Que nenni ! J'en ai profité pour passer commande des circuits imprimés et des composants ! Seul problème, une rupture de stock sur un des composants, que je n'avais pas remarquée en passant commande (ça m'apprendre à faire les choses à 5h du matin avant d'aller me coucher, tien...)
Et il y a quelques jours, me voila avec ceci dans les mains !
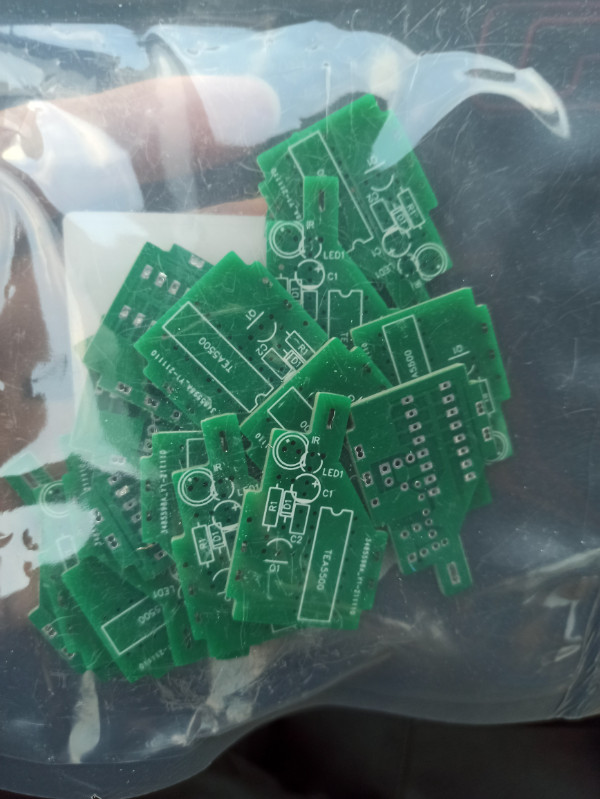
Hier, j'ai assemblé les composants en ma possession et les circuits, et voilà le résultat ce soir après soudure


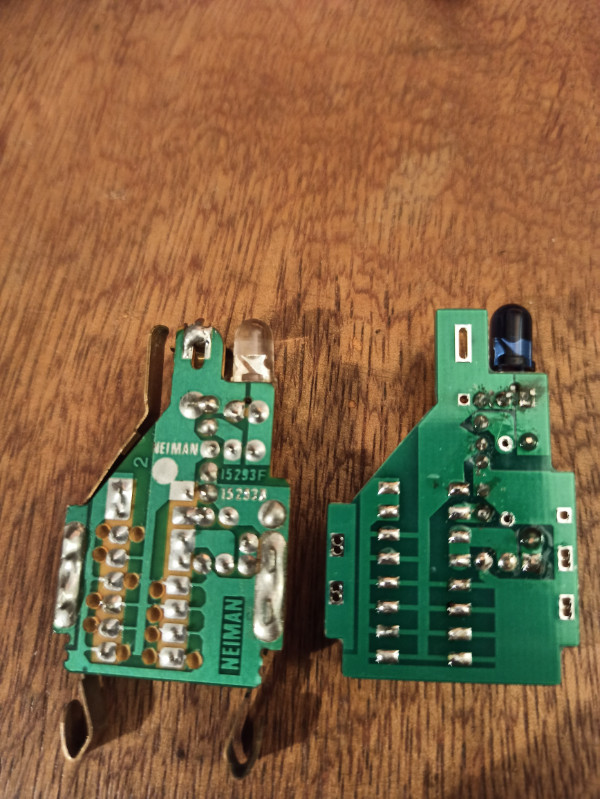
C'est loin d'être parfait, il s'agit d'un premier prototype, qui devra être corrigé et adapté pour correspondre au cahier des charges que je me suis fixé : être au plus proche de l'original que possible.
Le circuit est trop épais de 0.2mm, et ne rentre pas en hauteur dans le boîtier d'origine
la diode infrarouge est noire et pas transparente comme à l'origine. Petit détail, mais les diodes avec ces caractéristiques n'existent plus en transparent.
le nouveau circuit a les deux faces vertes, mais l'original n'en a qu'une. détail aussi, mais dû aux technique de fabrication
il me manque un composant, qui était en rupture de stock, et que je n'ai pas eu le temps de re-commander
je n'ai pas les accessoires qui accompagnent le circuit imprimé (guide de la diode infrarouge et connexions en cuivre) car je n'ai pas encore réfléchi à comment me les procurer (des idées ?)
la partie haute du circuit imprimé n'est pas arrondie comme sur l'original, mais carrée (je ne pensais pas que ça aurait une incidence, mais après vérification si. ça passe assez juste dans le boîtier, et sans cet arrondi, c'est prendre un risque inutile si je peux modifier ça dans mon fichier informatique.
Cela dit, pour un premier jet, c'est pas si mal !
Les dimensions sont bonnes, il va pouvoir s’emboîter parfaitement dans le boîtier d'origine
l'emplacement des perçages est bon, tous les composants peuvent être assemblés sur le circuit imprimé
Les composants sont ceux que j'ai commandé, et les références correspondent
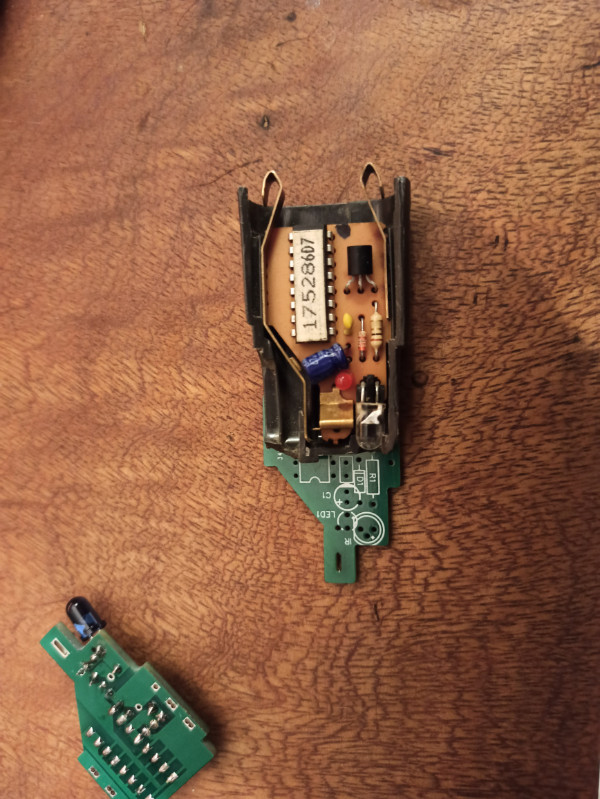
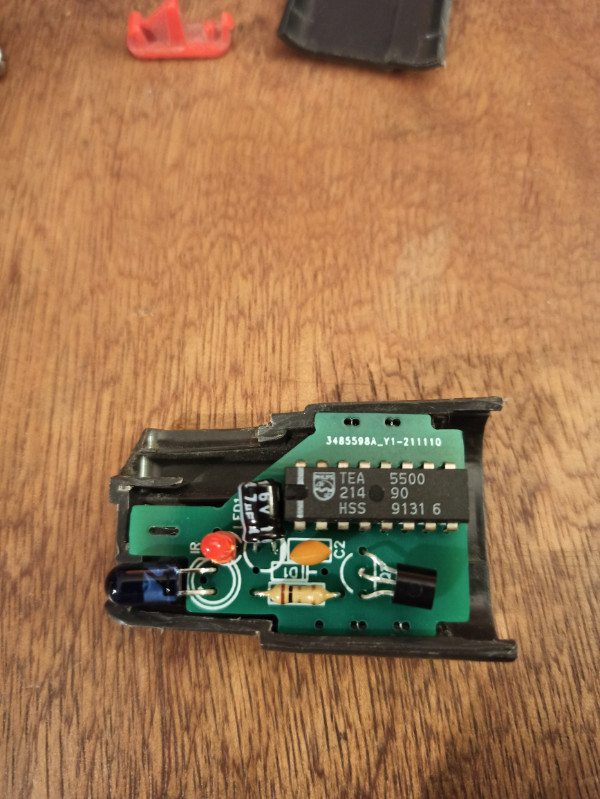
Voilà ou j'en suis ce matin.
J'avais envie de partager l'avancée de ce projet, qui commence à se concrétiser, et qui à minima permettra a qui veut d'ouvrir sa 205 à distance.
Et j'avoue que sur certains points, je solliciterais bien l'avis du public :
- le guide de la LED infrarouge : je n'ai aucune idée de comment ça s'appelle, de ou le trouver, ou sinon de quelle technologie serait assez précise pour le fabriquer
- les connexions en cuivre : acheter des bandes de cuivre ? faire découper au laser ? on en trouve sur les sites de composants, ou c'est vraiment unique ?
- le boîtier : impression 3D ? moulage ? quel coût, quelle qualité, quelle finition ?
- la série : je me doute bien que je ne vais pas en écouler autant que de 205 encore sur nos routes, mais je ne vais pas en faire que 10 non plus. donc sur une échelle de quelques centaines de pièces, si quelqu'un travaille dans l'industrie, est-ce envisageable de confier l'assemblage à une entreprise ?